The best wholesale plastic bottle and its supplier’s uses
- qualityblowmoulder
- Aug 23, 2022
- 3 min read
Plastic bottle production is done in phases. Plastic bottle producers typically make bottles out of one of four different types of plastic. Although polyethylene terephthalate is both robust and lightweight, it is commonly used to make plastic bottles that store potable water and other beverages.
Polyethylene is used to make stiff plastic bottles such as detergent bottles in their increased form and squeezing bottles in their low-density version. Polypropylene is commonly used in pill bottles and other similar applications. Rechargeable water bottles and other reusable containers are made of polycarbonate. To comprehend the production processes, it is necessary to first evaluate the compositions of the materials used.
PET evaluation
Polyethylene Terephthalate is a polymeric material that, depending on the specific material characteristics of Plastic Bottle Wholesale, can be either opaque or transparent. PET, like other polymers, is made from petroleum hydrocarbons by a combination of ethylene glycol and terephthalic acid. The PET is polymerized to form a long polymer structure, allowing it to be used to make PET bottles later on.
Polymerization is a sophisticated process that accounts for many of the differences between batches of produced PET. During polymerization, two types of contaminants are often produced: propylene glycol and acetaldehyde. Although diethylene glycol is not normally created in sufficient quantities to harm PET, acetaldehyde can be formed not just during polymerization but also during the bottle production process.
The PET bottle production process may begin after the plastic has been made. To verify that the plastic is safe for usage, many tests are performed after manufacture to confirm that the bottles are not permeable to carbon dioxide. Visibility, gloss, shatter strength, density, and pressure opposition are all carefully checked.
Polypropylene resin is a low-density, generally opaque polymer with outstanding thermoforming and insertion molding properties. It competes largely with polyethylene for bottles and can be made visible for see-through uses, whereas polyethylene can only be made semi-transparent, as in milk jugs. Wholesale Plastic Bottle Suppliers cannot compete with the optical clarity of polyethylene such as polycarbonate, yet it performs admirably. Because of its low viscosity at melt temps, it is ideally suited to extrusion and molding processes such as blow molding.
Polycarbonates are created by the synthesis of bisphenol and phosgene. Because it is more expensive than other bottle-making polymers, it is generally used in high-end reusable containers such as nursing containers or those seen on water coolers or in scientific settings. The material has outstanding optical qualities and strength, making it perfect for bottles that must have the clarity of glass while also being able to withstand repeated, and occasionally rigorous, treatment. The material is a cryogenic process and can endure multiple items of washing.
Molding Bottles Should Be Reheated and Blown
Investment casting is the first stage of a conventional two-step Heat it up and Blow Machine (RBM) bottle production process. Plastic Bottle 500ml pellets are polymerized in the cylinder of an injection molding process, where heat and the combing action of feed screws melt the plastic. The plastic is then pumped into molds with many cavities, where it takes on the shape of long, small tubes. These tubes, known as parisons, often feature the preformed necks and threads that will be used to cap the upcoming bottles. Because PET parisons, or pre-forms, are significantly more compact than fully formed containers, they are readily delivered to bottling operations.
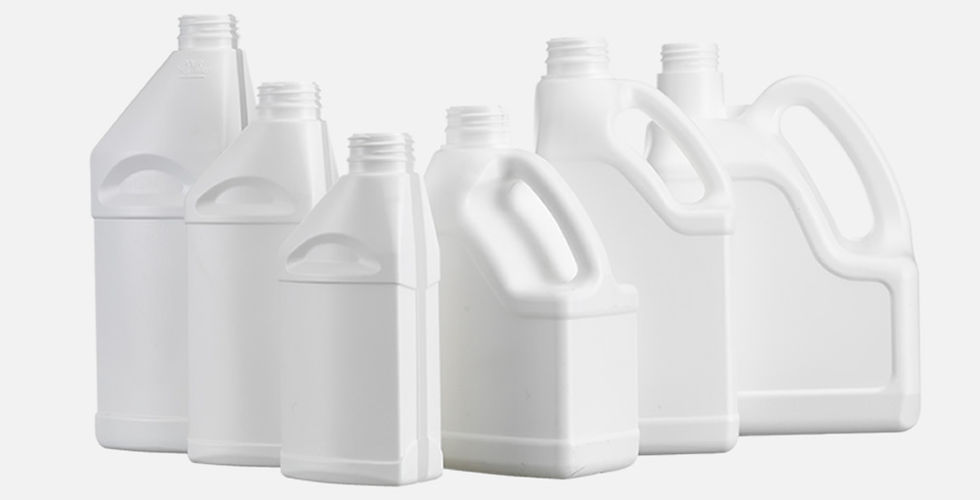
The parisons are fed into a distribution system and processed through an approach when it comes even during the re-heat process, which orients the parisons for trying to feed into the blow molding machine. The parisons are preheated by running them via quartz heaters before entering the mold.
A thin steel rod, known as a mandrel, is inserted into the neck of the parison, where it fills the parison with highly pressurized air. Stretch blow molding begins: the parison is blown and extended into the mold axially and outwards as a direct consequence of the pressurized air, heat, and pressure, forming a bottle shape. This procedure yields a bi-axially oriented container with a CO2 barrier that is perfect for storing sweetened beverages. For more information Contact Us now at our website.
Comentarios